REPORTS
CONTENTS |
|
1. General
Profile
Product profile
Productivity index and cost analysis
2. Stakeholder's perception
3. Environment policy and
management systems
4. Mining
5. Process management
Raw material sourcing, characteristic,
handling and consumption
Raw Material Processing
Pyroprocess
Cement grinding, packaging and storage
6. Energy consumption, energy generation
efficiency and its benchmarking
7. Water sourcing, consumption and its
benchmarking
8. Air pollution and emission control
systems
Air pollution monitoring
Air pollution load and its benchmarking
Emission control equipments
9. Solid waste management
10. Conclusion |
|
|
|
General Profile
This section gives a general overview of the company
- its location, its product profile, its financial performance and its workforce
productivity. Contains information benchmarking the
company's workforce productivity with international players like Lafarge and Holcim
and expenditure of the company on raw material,
energy and workforce. |
go to top
|
|
|
|
Stakeholder perception
This section contains information on the how various
stakeholders like villagers living near the production plant as well as the mines,
Pollution Control Board officials, local media etc. view the environmental performance of
the unit. Often, local communities act as effective barometers of environmental
performance. 1 |
go to top
|
|
|
|
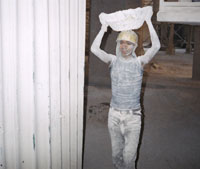 |
Worker in the
packaging section. Plants rarely enforce the use of protective equipment |
Occupational health and environment management systems
This section documents the performance of the company
in setting up effective systems to ensure good environmental performances - for example,
adopting a forward-looking environment policy and giving a strong as well as extremely
clear mandate to the environment department. Occupational health is a major issue with the
sector. This section documents the initiatives taken by the company, such as expenditure
on occupational health and safety.
|
go to top
|
|
|
|
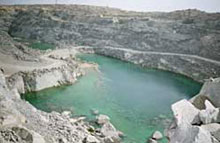 |
Three-fourths of the
exhausted area in the mines are going to be 'water reservoirs' - essentially pits. |
Mining
Mining is without doubt the most ecological destructive part of the cement life cycle.
This section looks at the location of the mine vis-à-vis its ecological and social
sensitivity, mine management and various steps the company has taken to reduce the impact
of mining including rehabilitation.
|
go to top |
|
|
|
Process management
This section looks at the company's performance right
from the processesing of various raw materials to the packing and dispatch of the product.
Contains useful information such as benchmarking
utilisation of waste materials at the company, thermal
energy consumption in the kiln, initiatives to control fugitive dust, and the level of
technology. |
go to top
|
|
|
|
Energy
consumption
A cement plant is a huge energy guzzler -
both of electrical as well as thermal energy. This section benchmarks the company's energy consumption and power
consumption with international players. |
go to top
|
|
|
|
Water
consumption
Though cement manufacturing is not water
intensive, the sheer size of the plants means huge consumption of water, and therefore a
strain on the local water resources. This section provides information on water
consumption and benchmarks this with the best in
the sector.
|
go to top
|
|
|
|
Air pollution
This section contains in-depth information on air pollution monitoring, dust loads and
greenhouse gas emissions. It also provides detailed information on dust emissions from the various point sources and
pollution control equipments installed.
|
go to top
|
|
|
|
Solid waste
The cement industry does not generate lot of
solid waste, which mostly comprises of refractory bricks, fly ash from power plants and
furnace oil. This section deals with the generation and management of the solid waste
produced by the production plant. |
go to top
|
|
|
|
Conclusion
Summarizes the environmental performance of the plant by highlighting its
strengths and weaknesses. |
go to top
|