...THE
IMPACT
The success of GRP depended not only on the participation and
disclosure of data but also on industry paying heed to the rating and its recommendations.
Before the rating of pulp and paper sector began, despite developing a robust and
transparent model of GRP, CSE had doubts about the success of the project in India. Indian
industry was notorious for turning a near-deaf ear to regulations and regulators.
Therefore, it seemed unlikely that CSEs GRP would prick the conscience of the
industry.
However, on all counts, CSE was in for a pleasant surprise. The
relevance of the entire exercise was realised in actual terms when a large section of the
pulp and paper industry, acknowledged and adopted many of the recommendations specifically
given to each company by the project.
 |
The project is using a discrepancy policy to penalise companies
who provide wrong information. |
 |
|
Rating of the Pulp and Paper Sector
The sample All pulp and paper production plants with more than 100 tonnes per day (tpd)
production capacity were selected for the rating. The sample consisted of 28 production
units of 23 companies spread across 13 states.
The ratings Overall the sector had performed very poorly with only
2 companies getting 3 leaves award while 13 companies were in the two leaves category and
as many as 12 companies in one leaf category (see Table 1.1). Though the poor
performance of the pulp and paper industry was something that GRP expected from the very
beginning, the finding of the rating was totally unexpected and a true eye-opener.
indings In comparison to some industries like mining, which are
inherently unsustainable, because the natural resources they exploit are non-renewable,
the pulp and paper industry seems less environmentally damaging. In practice, however, the
project found out that the pulp and paper industry is a voracious consumer of natural
resources like water, wood fibre and energy and during production and disposal stages, a
large proportion of these come out in the form of waste. The project also found that the
sharp contrast between pulp and paper companies of India and that of developed world is
because of the use of obsolete technology and the small size and capacity of the Indian
mills. The major findings of pulp and paper sector rating is summarised below:
Name |
Installed
capacity
(in MT/annum) |
State |
Weighted
score (%) |
Ranking/Rating |
J K Paper Mills |
90,000 |
Orissa |
42.75 |
1 |
Andhra Pradesh
Paper Mills Ltd |
98,500 |
Andhra Pradesh |
38.50 |
2 |
Sinar Mas Pulp
& Paper (India) Ltd |
1,15,000 |
Maharashtra |
37.40 |
# |
BILT-Ballarpur Unit |
1,50,000 |
Maharashtra |
33.44 |
3 |
Hindustan Newsprint
Ltd |
1,00,000 |
Kerala |
33.30 |
4 |
SIV Industries Ltd |
60,000 |
Tamil Nadu |
31.73 |
5 |
Pudumjee Pulp &
Paper Mills Ltd |
33,000 |
Maharashtra |
31.44 |
6 |
Tamil Nadu
Newsprint & Papers Ltd |
1,80,000 |
Tamil Nadu |
31.40 |
7 |
ITC-Bhadrachalam
Paperboards Ltd |
62,500 |
Andhra Pradesh |
31.15 |
8 |
Century Pulp &
Paper |
Century Pulp &
Paper 1,51,920 |
Uttar Pradesh |
31.07 |
9 |
HPCL-Nagaon Paper
Mills |
1,00,000 |
Assam |
28.70 |
10 |
Seshasayee Paper
& Boards Ltd |
60,000 |
Tamil Nadu |
28.20 |
11 |
The West Coast
Paper Mills Ltd |
1,19,750 |
Karnataka |
27.67 |
12 |
BILT-Asthi Unit |
35,000 |
Maharashtra |
27.10 |
13 |
BILT-Yamunanagar
Unit |
70,000 |
Haryana |
25.70 |
14 |
The Central Pulp
Mills Ltd |
45,000 |
Gujarat |
25.35 |
15 |
Star Paper Mills
Ltd |
53,000 |
Uttar Pradesh |
24.76 |
16 |
Shree Vindhya Paper
Mills Ltd |
33,000 |
Maharashtra |
24.70 |
17 |
BILT-Sewa Unit |
30,000 |
Orissa |
23.75 |
18 |
Orient Paper Mills |
85,000 |
Madhya Pradesh |
22.10 |
19 |
The Mysore Paper
Mills Ltd |
1,30,000 |
Karnataka |
21.60 |
20 |
Cachar Paper Mills |
1,00,000 |
Assam |
21.43 |
21 |
Rama Newsprint
& Papers Ltd |
61,380 |
Gujarat |
21.10 |
22 |
BILT-Chaudwar Unit |
20,000 |
Orissa |
21.06 |
23 |
Nath Pulp &
Paper Mills Ltd |
41,750 |
Maharashtra |
20.80 |
24 |
Grasim Industries
Ltd (Mavoor) |
57,600 |
Kerala |
20.65 |
25 |
Mukerian Papers |
34,650 |
Punjab |
20.01 |
26 |
Amrit Paper |
26,400 |
Punjab |
19.01 |
27 |
#Sinar
Mas was operational since 1996-97 only and thus its environmental performance could not be
compared with that of other mills. |
A mill with a capacity of 33,000 tonnes
per annum (tpa) is considered to be large in India, compared to Brazil and Sweden where
the large mills have a capacity between 300,000 to one million tpa. This poses potential
financial problems for Indian companies for upgrading technology to reach international
standards environmentally.
 |
The objective of GRP is not only to rate the
environmental performance but also recommend ways to improve performance |
 |
|
The
potential use of wastepaper is evident from the fact that mills in South Korea and Taiwan
are entirely dependent on wastepaper as a raw material. About 12-13 million tonnes or 14
per cent of the worlds consumption of wastepaper is traded internationally, of which
50 per cent is provided by the US. In India, a majority of paper mills (63 per cent) use
wastepaper as a raw material. They account for 30 per cent of the paper manufactured in
the country. However, most of the wastepaper is imported from countries like USA as the
domestic recycling rate is very poor.
Majority
of Indian mills still use elemental chlorine for bleaching and that too in an extremely
inefficient manner. The organochlorine discharged due to chlorine bleaching process enters
the food chain and does not degrade easily. In India, not even one state pollution control
board has facilities to test organochlorine and in practice, this parameter has not been
used by them to monitor
industrial discharge. Very few companies have ever monitored organochlorine in their
wastewater.
Fibre efficiency
While the Indian average in fibre efficiency is 32.4, the
world average is 52.5 per cent. Andhra Pradesh Paper Mills is only 0.2 per cent away from
meeting the world average |
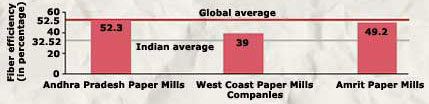 |
Water consumption
With 415 cubic metres (cum) requirement to make one tonne
of paper, Ballarpur Industries Ltds Shree Gopal unit is a class apart. The world
average is only 55 cum |
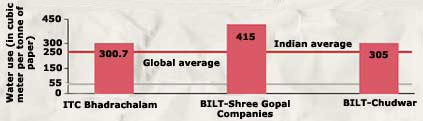 |
Fibre
requirements of the pulp and paper sector are met by bamboo, hard wood, agro waste and
wastepaper. The amount of land required by a mill to meet its raw material needs equals
the ecological burden that the mills fibre sourcing has on the environment. The average
Indian mills footprint is 2.17 hectare (ha) for every tonne of paper it produces. Taking
the total annual production to be around 3.2 million tonnes, the total land requirement of
the Indian pulp and paper sector would be 6.7 million ha.
There is a considerable dependence of Indian mills on government
forest as majority of the raw material are being outsourced from them.
Water
comes extremely cheap to the Indian mills and therefore there is no attempt to regulate
its use. Hence Indian pulp and paper mills have very high water consumption.
|